

OEE is the Overall Equipment Effectiveness of a defined production process during the defined operative period or mode in which all activities related to production, personnel and inputs are accounted for during all producing or dependent activities within a defined scheduled time or operative mode time. The idea is to present a common definition and straightforward spreadsheet format to bring about clear, common approach. Although the concepts are fairly simple, their definitions and application have varied considerably, preventing any ability to use them as benchmarks and performance tools within and between plants, let alone between companies. OEE and its basic approach have been around for decades in other industries and have recently moved into the packaging area. It gives a common language to everybody involved in manufacturing and leads to effective and efficient improvements. OEE helps to create this kind of awareness with operators, with engineers, with logistic departments, and with anybody else involved in the value adding process. Likewise, “I stopped for 5 minutes” is the same as “I lost 200 potential bottles I should have made”. Most operators will not say ‘Today I ran at a takt time of 1.5 seconds but instead “today I ran 40 products per minute” - which is the same thing. OEE is purely time based (time converted), but since 1 takt time equals 1 bottle, OEE can be calculated in bottles for ease of use. At the end there were 9,000 bottles that were saleable, so the Overall Equipment Effectiveness was 31.25%.Īvailability (62.5%) x Performance (66.7%) x Quality (75%) = 31.25% Theoretically we could make 480 x 60 = 28,800 bottles. The rest of the time the machine is in the running mode.īreaks = 10 minutes morning + 30 minutes lunch + 10 minutes afternoon = 50 minutes Our operators take 10+30+10 minutes in breaks as well as do 2 changeovers of 35 minutes each and lose 60 minutes of machine downtime during the shift. Going back to the bottle example, let’s track down a normal day.
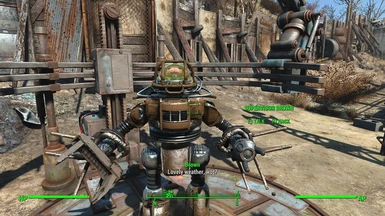
So how do we find out what we lost and where? And how do we prevent it from happening in the future? Making it at the right time – producing as planned, keeping the machine up and running, minimizing time losses (Availability) Making it the right way – no rework, no defects, no waste (Quality) Making the right thing – the right product or SKU at the right speed (Performance)
Fully upgraded automatrons losing all equipment full#
If we lose 14,400 products because the machine ran flawlessly, with no quality loss but at half the maximum speed, that’s completely different from producing 28,800 products at full speed, and then dumping 14,400 out-of-spec products into the landfill. Every day that we run 50% OEE, we can lose units in different ways, and every loss has its own cost structure. OEE, when broken into its three main components, is going to track down where we lost it.
